重型卡车的驱动桥总成设计(英文版)(含CAD零件图装配图,STEP三维图)(任务书,开题报告,文献摘要,外文翻译,论文说明书英文版9000字,CAD图6张,STP三维图)
Design of driving axle of heavy truck
ABSTRACT
Drive axles as one of its four Assembly vehicles, which have a direct impact on the performance of vehicle performance, and load goods vehicles is very important. When using the high power output of the engine torque to meet current fast and heavy-truck when the need for efficient, cost effective, must be used with an efficient, reliable drive axle. Design structure is simple, reliable, low cost drive axle, can greatly reduce the total cost of vehicle production, promote the economic development of the automobile.
This design first expositions has driven axles of overall structure, in analysis has at home and abroad status, and driven axles the part structure form and past form of advantages and disadvantages of Foundation Shang, determine has overall design programme: used overall type driven axles, main reducer of deceleration type type used double level reducer, main reducer gear used spiral cone gear, differential used General symmetric type cone planet gear differential, half axis used full floating type, axles shell used casting overall type axles shell. In this design, the major completed a two-stage reducer, planetary gear differential, full floating axle with tapered design and check of axle of selection of materials and so on.
Key words: Driving axle;Design;Calculation;Checking;Material
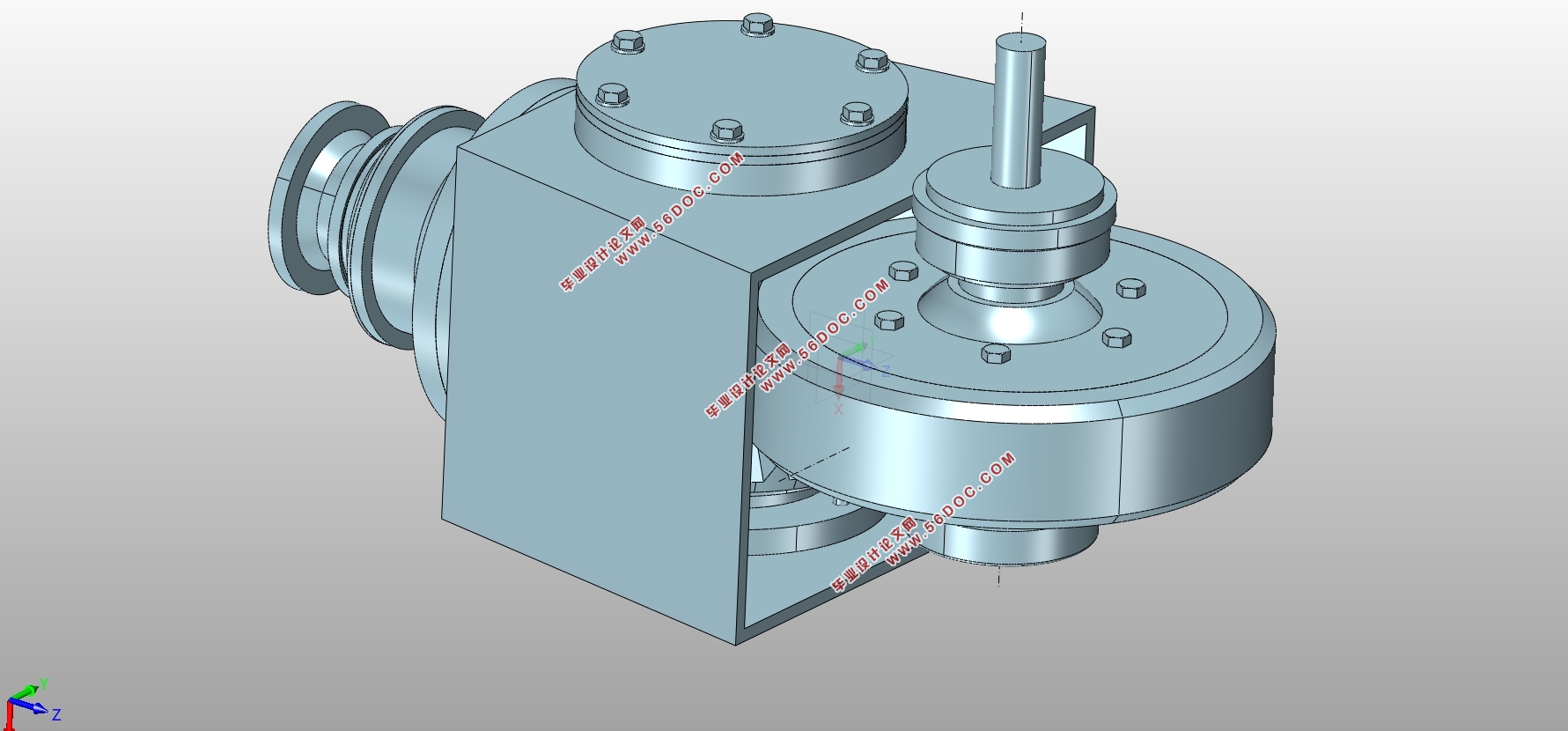
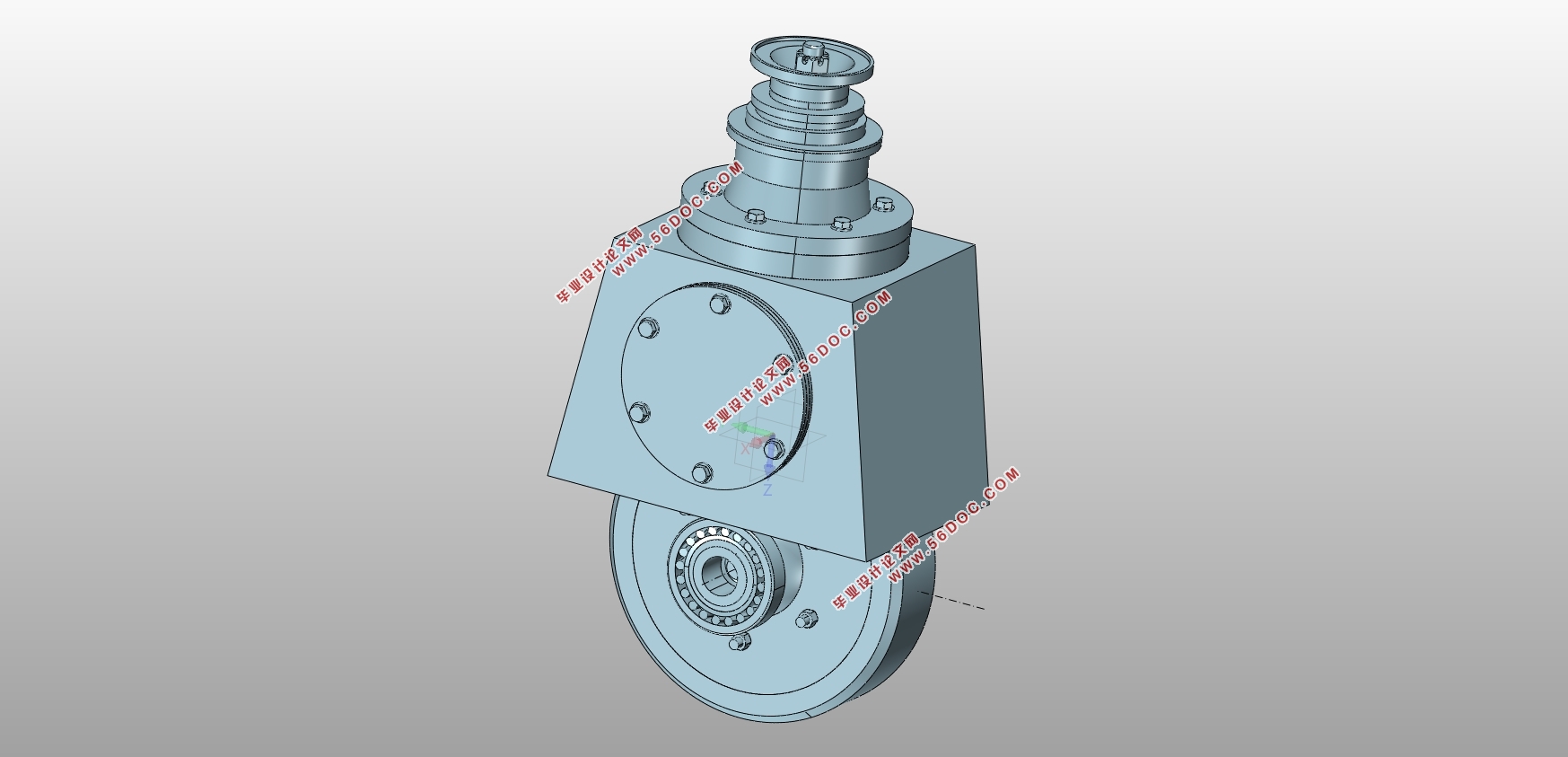
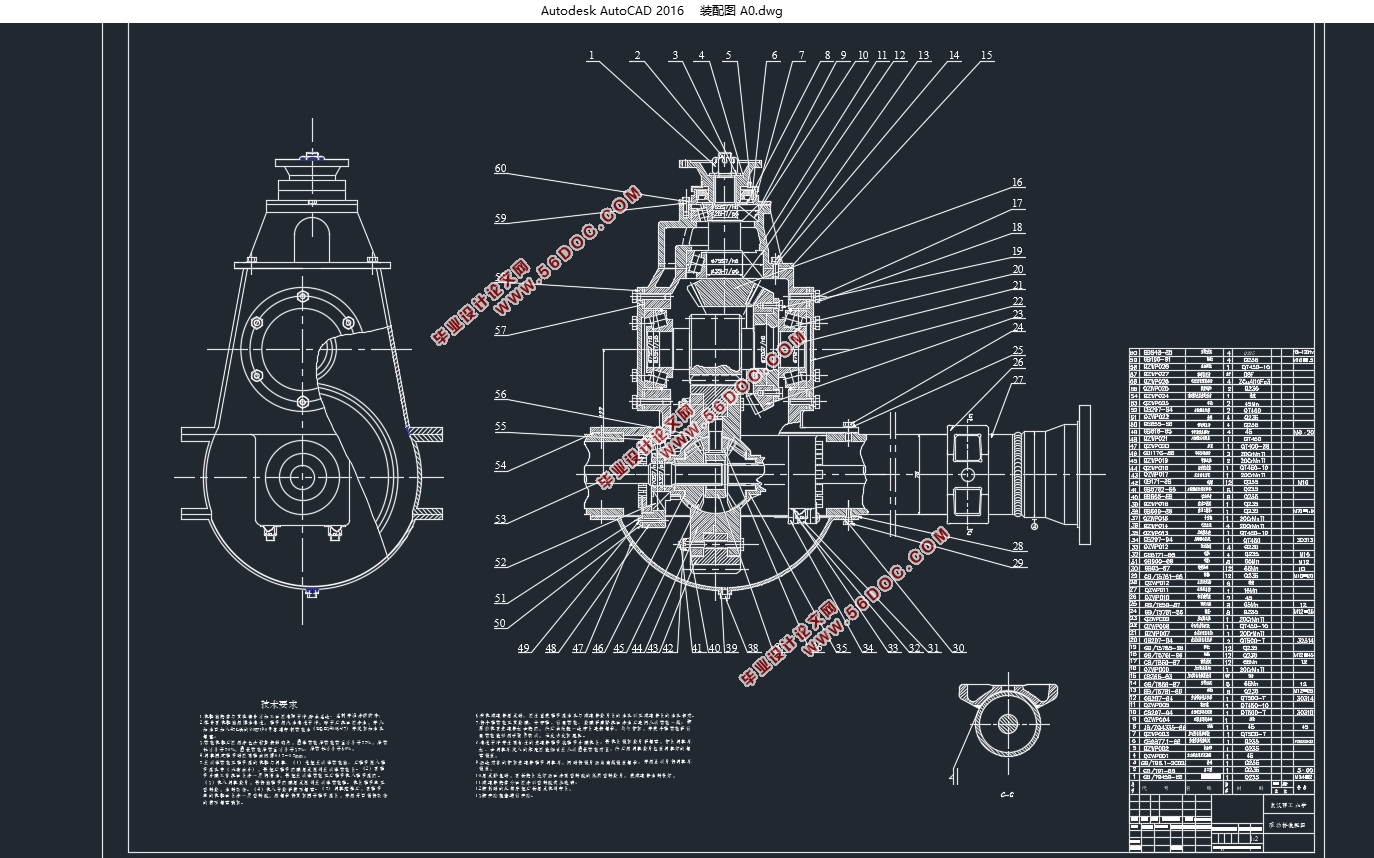
目录`
1 Introduction 6
1.1 Preface 6
1.2 Overview of automobile driving axles 6
1.3 Research Progress on driving axles at home and abroad 7
1.4 The basic contents, objectives and technical schemes of the research 8
2 Final reduction drive design 9
2.1 Analysis and determination of the structure scheme of the final reduction drive 9
2.1.1 Calculation of the ratio of the final reduction drive 9
2.1.2 Determination of the structure scheme of the final reduction drive 10
2.2 final reduction drive gear design 10
2.2.1 Determination of the calculation load of the gear of the final reduction drive 10
2.2.2 The selection of the gear parameters of the final reduction drive 12
2.3 The material and heat treatment of the gear of the final reduction drive 13
2.4 Calculation of spiral bevel gear of final reduction drive 13
2.4.1 Geometric size calculation of spiral bevel gear of final reduction drive 13
2.4.2 Strength calculation of spiral bevel gear of final reduction drive 15
2.5 Calculation of the bearing of the final reduction drive 16
2.6 Lubrication of the final reduction drive 19
2.7 Summary 20
3 The design of differential 21
3.1 Analysis and determination of differential structure scheme 21
3.2 Design of common bevel gear differential 21
3.2.1 Symmetric conical planetary gear differential 21
3.2.2 Selection of basic parameters of differential gear 22
3.3 Differential Gear Geometry Calculation and Strength Calculation 24
3.3.1 Differential gear geometry calculation 24
3.3.2 Differential gear strength calculation 25
3.4 Summary 26
4 Axle design 27
4.1Determination of semi-axle form 27
4.2Axle shaft design and calculation 27
4.2.1 Axle design 27
4.2.2 Design and calculation of full floating half shaft 29
4.3Structure design of semi shaft and material and heat treatment 29
4.4Summary 30
5 Drive axle housing check 31
5.1Determination of the form of axles shell of driving axles 31
5.2Stress analysis and strength calculation of the axles shell 31
5.2.1Calculation of static bending stress of a axles shell 31
5.2.2Strength calculation of axle housing under impact load of uneven road surface 32
5.2.3Strength calculation of axle housing when driving vehicle with maximum traction force 32
5.2.4Strength calculation of axle housing in emergency braking of automobile 33
5.2.5Calculation of the strength of the axles shell when the vehicle is subjected to the maximum lateral force 34
5.3Summary 37
6 Summary 38
|