2吨纯电动物流车一体式电驱动桥结构设计(英文版)(含CAD图,CATIA三维图)(任务书,开题报告,外文翻译,文献摘要,论文说明书英文版8000字,CAD图5张,CATIA三维图)
The structural design of the integrated electric drive axle of 2 tons pure electric logistics vehicles
Abstract
The mainstream trend in automotive research and development nowadays is electrification, and one of the keys to electrification for vehicle is the electrification of the drive axle. This design refers to the traditional truck drive axle design method, combined with the motor unit, to design a relatively reasonable integrated electric drive axle.
With the given data, design and analysis the overall parameters of vehicle.Determine the parameters of the motor to ensure that the power of the vehicle meets the needs of use.Determine the form of the final drive, choose the appropriate form to ensure that the structure of the drive axle is simple and small, design and calculate the reducer gears and check strength of it. Determine the form of the differential and do the design, calculation and strength check of the differential bevel gear. Select the suitable drive shaft, complete the design, calculation and strength check. Select the form of axle housing and combined with finite element analysis to check the strength of it.
After determining the parameters, use the modeling software CATIA to complete the 3D models about each parts ,export the 2D drawings, using CAD to modify and improve them. to ensure that the structure in the assembly drawing and part drawing is clear and complete.Finally, use the finite element analysis function of CATIA to complete the analysis of the electric drive axle about check strength and stiffness.
Key Words:electric drive axle; integrated design;CATIA;finite element analysis
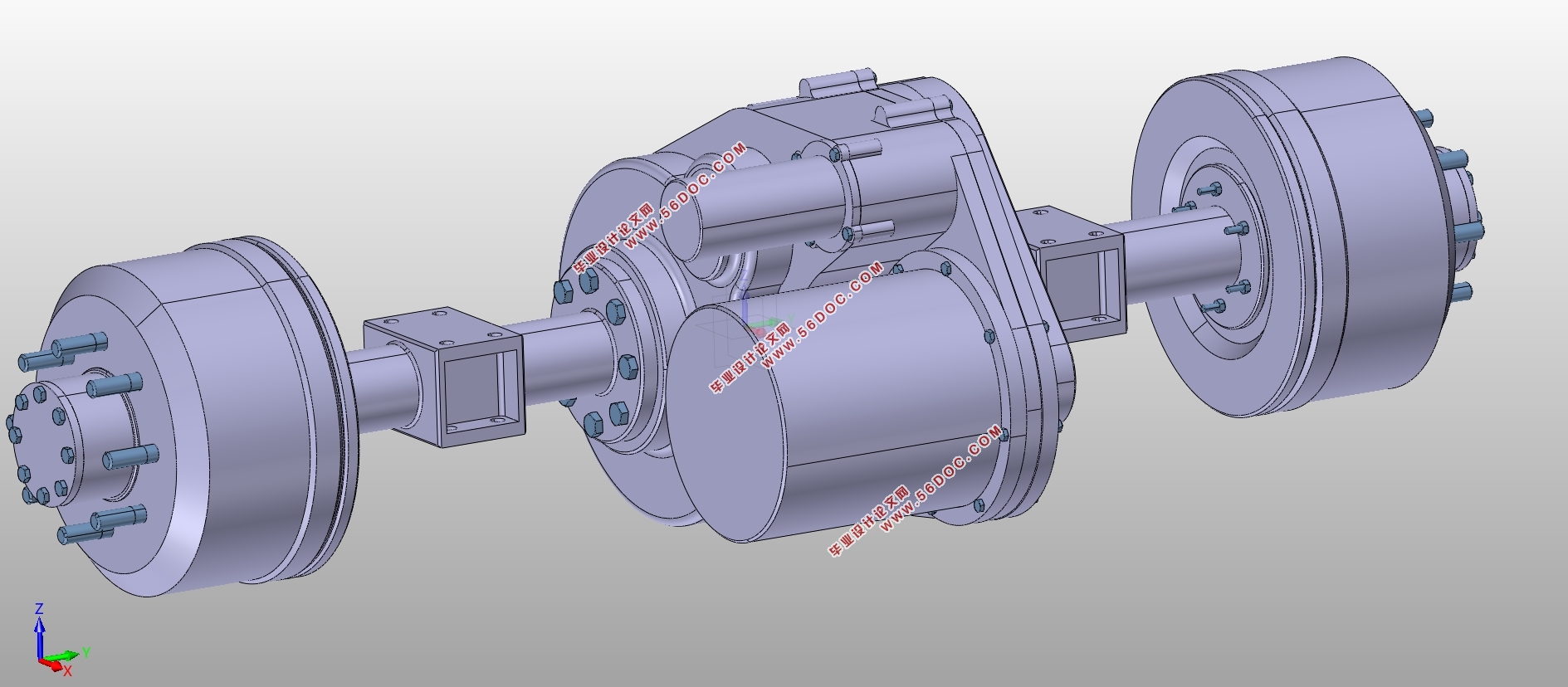
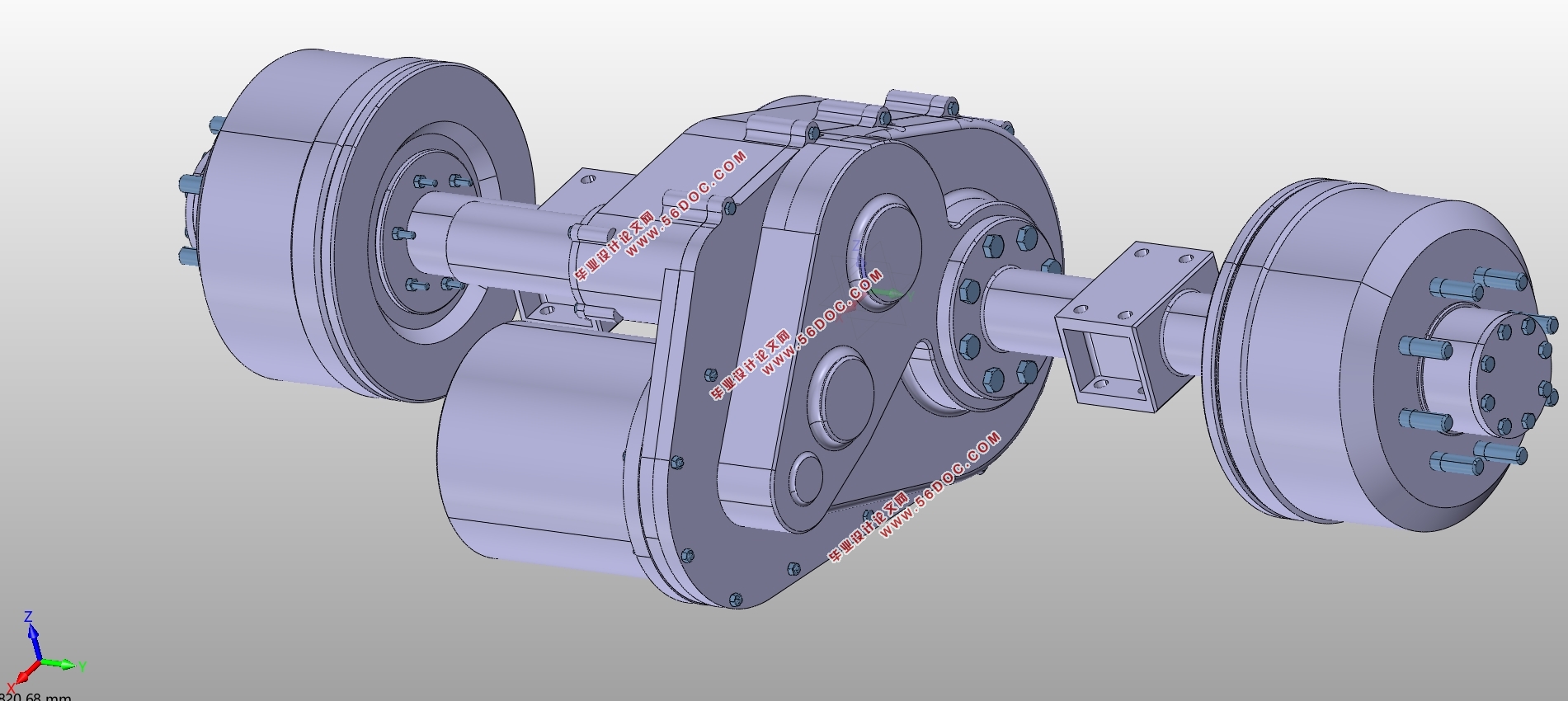
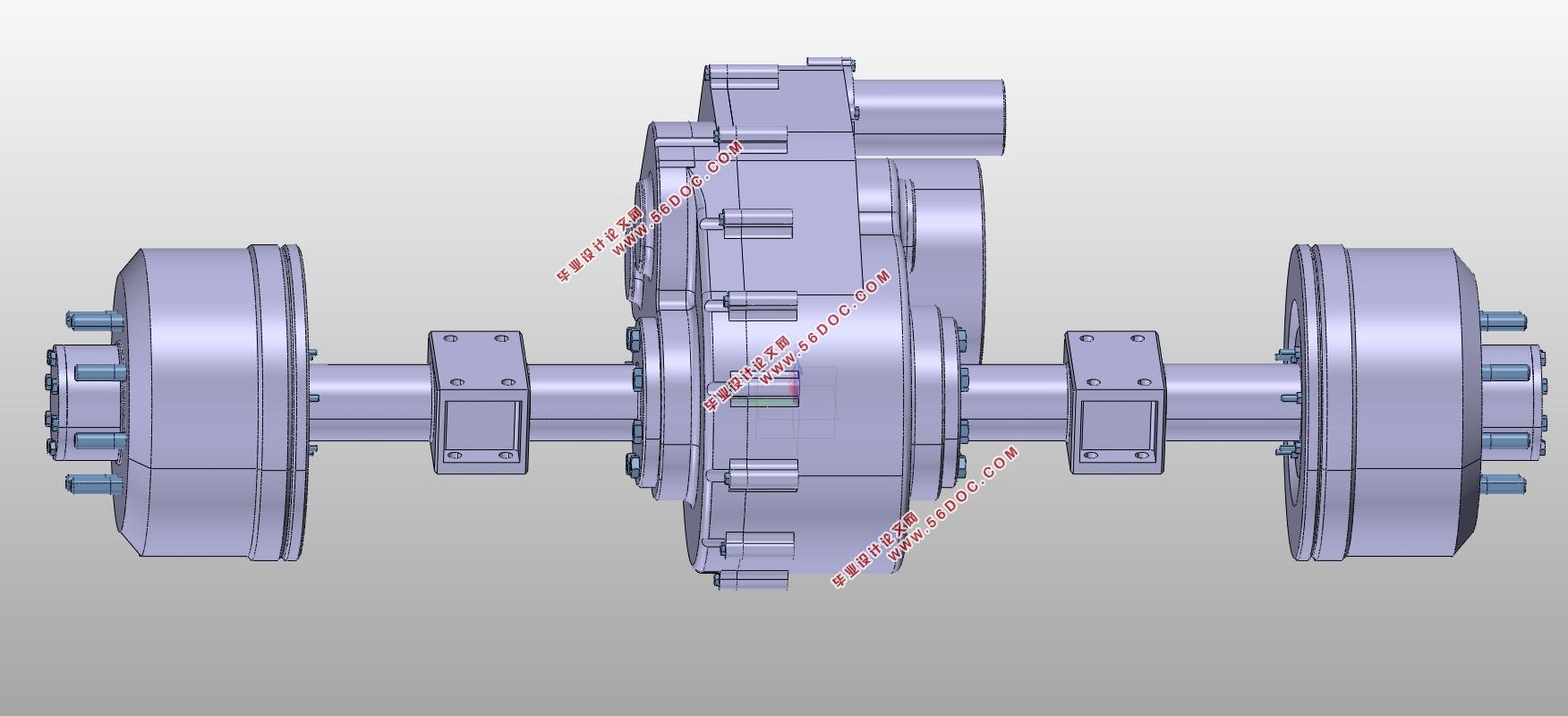
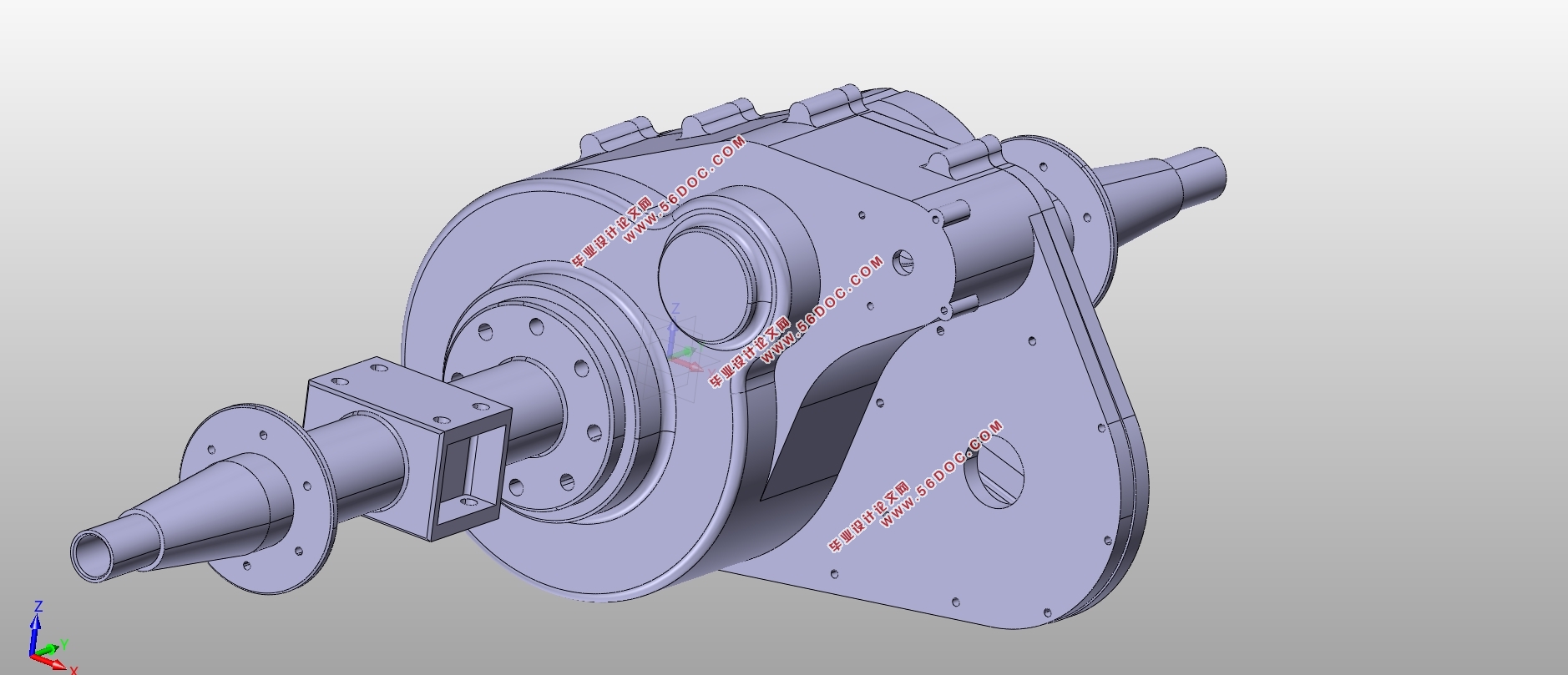
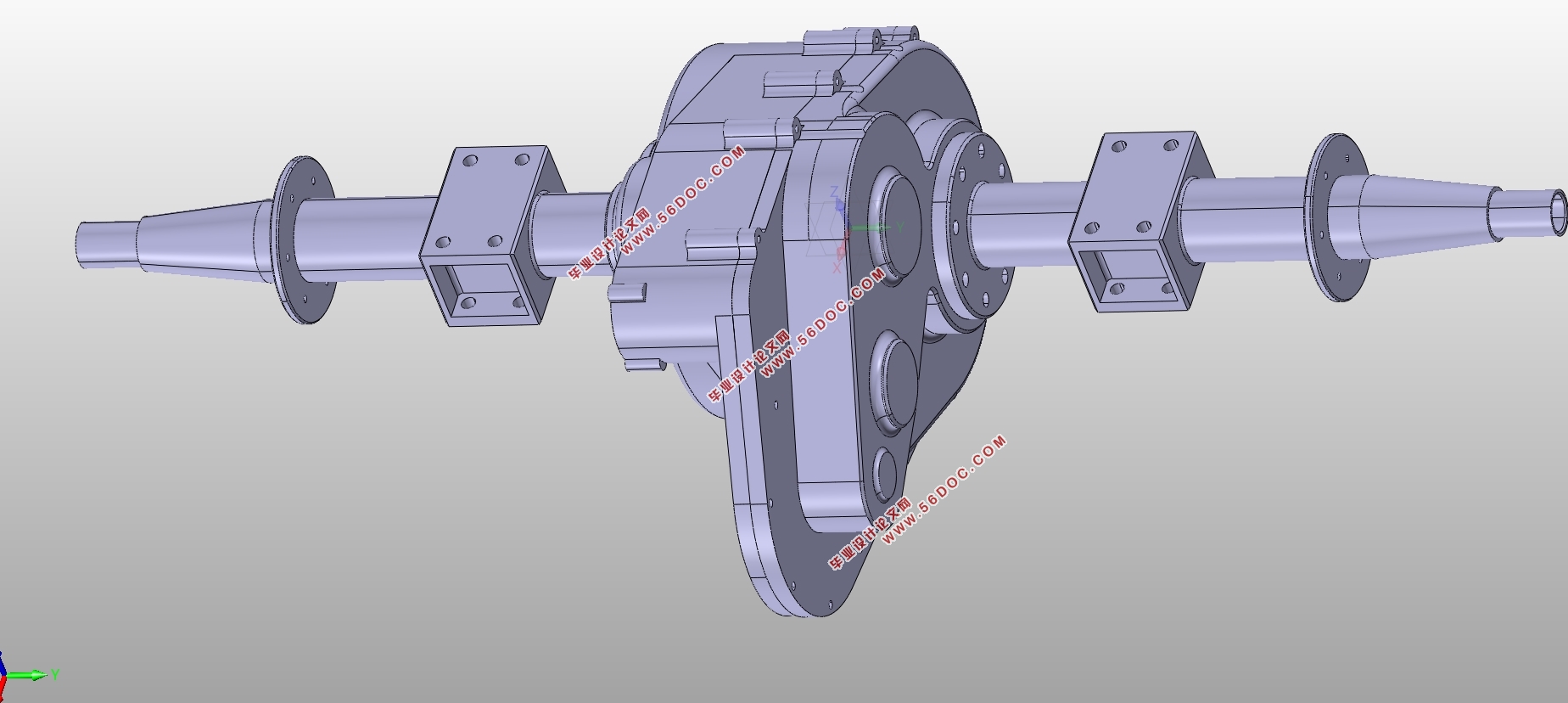
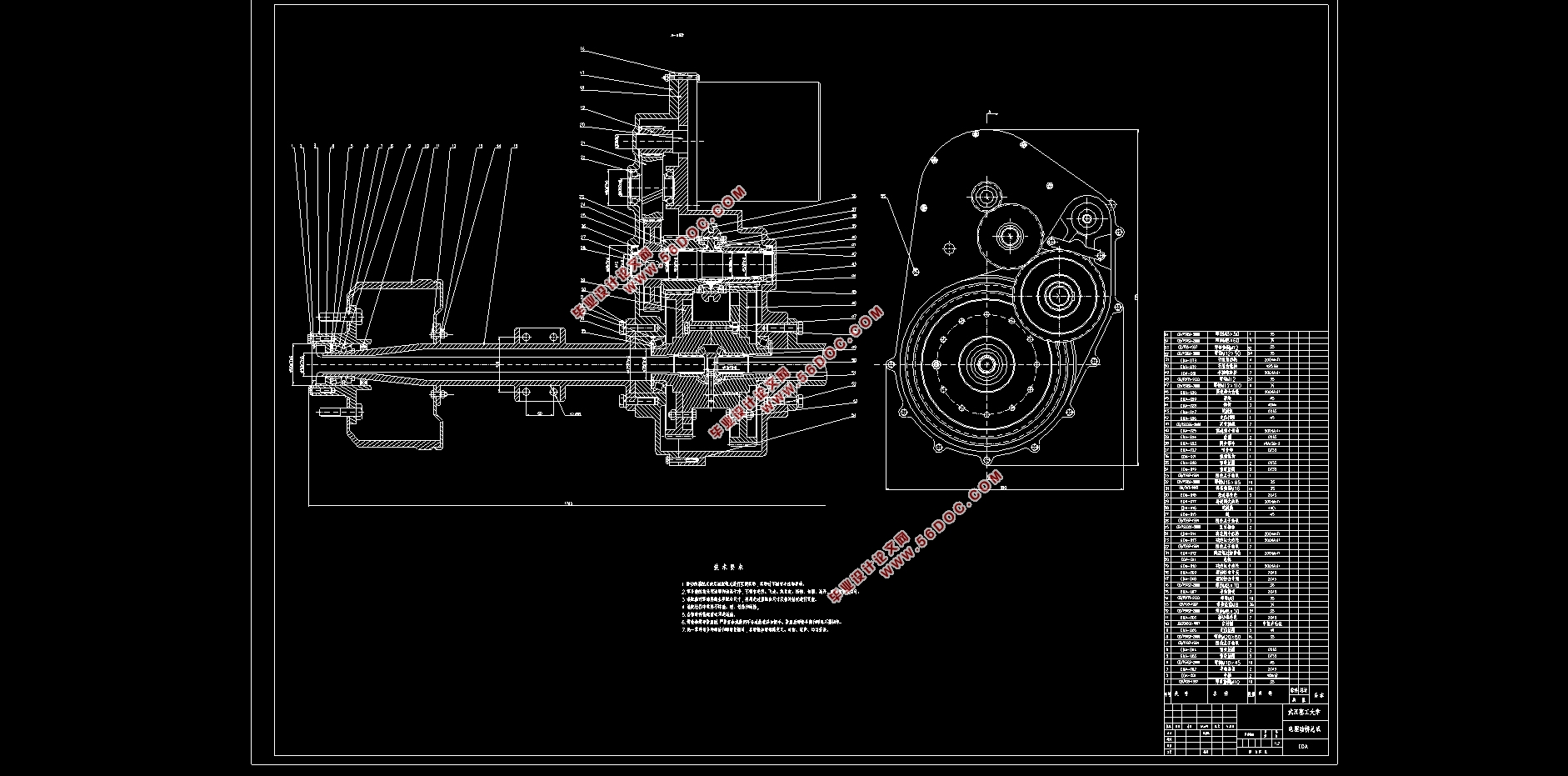

Contents
Chapter 1 Introduction 1
1.1 The purpose and significance of research 1
1.2Research Status at home and abroad 2
1.3Main research content 3
Chapter 2 The design of electric drive axle 4
2.1 The design of drive axle assembly structure 4
2.2 Determination of the final drive 4
2.2.1 Dynamic requirements of pure electric logistics vehicles 4
2.2.2 Selection of motor parameters and final drive ratio 5
2.3 The design of final drive 6
2.3.1 The structure of final drive 6
2.3.2Main parameters of reducer spur gear transmission 7
2.3.3 Main parameters of spur gear transmission of two-speed final drive 10
2.4 Design of differential 13
2.4.1 Structural form of the differential 14
2.4.2 Design of ordinary bevel gear differential gear 14
2.5 Design of drive shaft 17
2.5.1 Form analysis of drive shaft structure 17
2.5.2Structural design of full floating drive shaft 19
2.5.3 Strength calculation of full floating drive shaft 19
2.6 summary 20
Chapter 3 CATIA 3D modeling 21
3.1 Introduction of software CATIA 21
3.2 Modeling of final drive 21
3.3 Modeling of differential 21
3.4 Modeling of drive shaft 24
3.5 Modeling of drive axle housing 25
3.6 Modeling of drive axle 27
3.7 Summary 28
Chapter 4 Finite element analysis of drive axle housing 29
4.1 Constraint and force analysis of drive axle housing 29
4.2 Limitations of calculation methods 29
4.3 Establishment of finite element model 29
4.4 Material properties and meshing 29
4.5 Static strength analysis of drive axle housing 30
4.5.1 Introduction 30
4.5.2 Maximum vertical force condition 30
4.5.3 Maximum traction condition 32
4.5.4 Maximum braking force condition 33
4.6 Summary 35
Conclusion 36
References 37
Acknowledgement 39
|